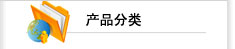 |
|
|
|
|
业务洽谈:
联系人:张顺平
手机:17727550196(微信同号)
QQ:3003262363
EMAIL:zsp2018@szczkjgs.com
联系人:鄢先辉
手机:17727552449 (微信同号)
QQ:2850985542
EMAIL:yanxianhui@szczkjgs.com
负责人联络方式:
手机:13713728695(微信同号)
QQ:3003207580
EMAIL:panbo@szczkjgs.com
联系人:潘波 |
|
|
|
|
 |
|
 |
当前位置:首页 -> 方案设计 |
|
|
C8051F850 BLDC马达参考设计 |
|
|
文章来源: 更新时间:2014/5/23 15:03:00 |
|
Silabs公司的C8051F85x/6x是嵌入高效增强性8051流水线架构CPU核的MCU,25MHzs时钟和高达25MIPS吞吐量,采用标准的8051指令集,闪存高达8KB,多达512B RAM,具有多达12路输入ADC,2个模拟比较器和片上调试,通信接口包括UART,SPI和I2C / SMBus,工作电压2.2V-3.6V,主要用在无刷DC马车驱动,FTTH和FTTH网络,传感器接口以及照明系统,机顶盒和投映仪.本文介绍了C8051F85x/6x主要特性,框图以及三相BLDC马达驱动系统模型图, C8051F850 BLDC马达参考设计主要特性,框图,动力板和MCU板电路图与材料清单.
The C8051F85x/6x MCUs are an ideal fit for low-memory, low-pin count applications. These MCUs feature a highly-efficient, enhanced 8051 pipelined architecture CPU core which executes 70% of the instructions in 1-2 system clock cycles.The C8051F85x/6x family takes functional density to the next level by integrating advanced analog, digital and communication peripherals as well as precision oscillators into highly cost-effective QFN20(3 mm x 3 mm), QSOP24 and SOIC16 packages. The MCU architecture also features a patented crossbar that enables developers to choose peripherals and pinout placement based on their application needs and layout constraints without worrying about the pre-set limitations and pin conflicts - allowing usage of small pinout packages, simplifying PCB routing, minimizing PCB layers and ultimately reducing design time, lowering system cost and most importantly optimal usage of pins. These on-chip features enable developers to minimize external components resulting in significantly reduced solution cost as compared to competitive MCUs.
C8051F85x/6x主要特性:
Memory
- Up to 8 kB flash
- Flash is in-system programmable in 512-Byte sectors
- Up to 512 Bytes RAM (256 + 256)
On-Chip Debug
- On-chip debug circuitry facilitates full speed, non-intrusive in-system debug(no emulator required)
- Provides breakpoints, single stepping, inspect/modify memory and registers
12-Bit Analog-to-Digital Converter
- Up to 16 input channels
- Up to 200 ksps 12-bit mode or 800 ksps 10-bit mode
- Internal VREF or external VREF supported
Internal Low-Power Oscillator
- Calibrated to 24.5 MHz
- Low supply current
- ±2% accuracy over supply and temperature
Internal Low-Frequency Oscillator
- 80 kHz nominal operation
- Low supply current
- Independent clock source for watchdog timer
2 Analog Comparators
- Programmable hysteresis and response time
- Configurable as interrupt or reset source
- Low current
General-Purpose I/O
- Up to 18 pins
- 5 V-Tolerant
- Crossbar-enabled
High-Speed CIP-51 μC Core
- Efficient, pipelined instruction architecture
- Up to 25 MIPS throughput with 25 MHz clock
- Uses standard 8051 instruction set
- Expanded interrupt handler
Communication Peripherals
- UART
- I2C / SMBus™
- SPI™
Timer/Counters and PWM
- 4 General-Purpose 16-bit Timer/Counters
- 16-bit Programmable Counter Array (PCA) with three channels of PWM, capture/compare, or frequency output capability, and hardware kill/safe state capability
Additional Support Peripherals
- Independent watchdog timer clocked from LFO
- 16-bit CRC engine
Unique Identifier
- 32-bit unique key for each device
Supply Voltage
- 2.2 to 3.6 V
Package Options
- 16-pin SOIC
- 20-pin QFN, 3 x 3 mm
- 24-pin QSOP
- Available in die form
- Qualified to AEC-Q100 Standards
Temperature Ranges:
- –40 to +125℃(-Ix) and–40to +85℃(-Gx)
C8051F85x/6x 应用:
Brushless dc motor
Electric tools
Small appliances
Battery chargers
Optical transceiver modules (FTTH)
FTTH (Fiber-to-the-Home) networks
Sensor interfaces
Lighting systems
Motor control
Set-top boxes
Stepper motor
Projectors

图1. C8051F85x/6x框图
C8051F850 BLDC马达参考设计
The Silicon Labs C8051F850 Sensorless Brushless dc (BLDC) Motor Control Reference Design is a ready to use motor control solution with production-quality hardware and software for quick evaluation and deployment in cost-sensitive applications. This reference design provides a complete system-level solution for sensorless brushless dc motors and is a vehicle for developers to evaluate and adopt low-cost BLDC motor control solutions using the C8051F85x/6x product family.
The C8051F85x/6x family is the ideal MCU for the reference design, with a 12-bit analog to digital converter, a precise internal voltage reference, two analog comparators with programmable hysteresis and response time and three independently configurable enhanced resolution PWM channels with built-in hardware kill capability.
The availability of motor control source code helps to expedite the design-in time. In addition, the motor control graphical user interface (Silicon Labs Spinner) allows real time control and monitoring of the motor and also offers users flexibility and ease of use when controlling and understanding the BLDC motor operation. A strong value proposition of the Sensorless BLDC Motor Control reference design is the supporting environment from tools, development kits, software libraries and collateral. The reference design contains everything needed to get the motor spinning in less than five minutes.
C8051F850 BLDC REFERENCE DESIGN KIT
This design kit provides a complete system-level solution for sensorless, brushless dc (BLDC) motors. This application note includes complete schematics, PCB layouts and firmware.
C8051F850 BLDC马达参考设计主要特性:
This kit supports 3-phase BLDC motors that meet the following specifications:
Trapezoidal back-EMF
Max operating voltage of between 10 V to 24 V dc
24 kHz PWM frequency
Maximum average current of 10 A
Maximum speed not exceeding 200,000 rpm for a 2-pole BLDC motor
Overcurrent detection capability stops the motor when average current exceeds 10 A.
Motor Stall detect capability stops the motor when a motor stall is detected or extreme loads encountered.
Tachometer Frequency Generator (FG) output signal
The kit aims to demonstrate the capabilities of the C8051F850 for operating BLDC motors. The unique features offered by this MCU for BLDC motor operation are:
PWM synchronized blanking of comparator for BEMF Zero-Crossing Detection
Automatic PWM duty cycle reduction to limit motor current during startup
Hyperdrive mode to increase the maximum speed of some motors
The kit consists of the following:
One MCU Board: MCRD-MCU-C8051F850 with the motor control firmware preprogrammed into the MCU
One Powertrain Board: MCRD-PWR-NLV-F85X
One BLDC Motor: Turnigy 450 Series 3800 kV Brushless Outrunner Helicopter Motor
One Motor Mount Board
One 8-bit MCU Kit CD
One 12 V, 5 Amp Universal Input Power Adapter

图2. C8051F850 BLDC马达参考设计外形图

图3. 三相BLDC马达驱动系统模型图

图4. C8051F850 BLDC马达参考设计框图
参考设计动力板
The powertrain board is designed to meet the following key motor specifications:
Motor supply voltage range of 10 to 24 V
Maximum average current of 10 amps
It consists of the following components that are relevant to this application:
6 IRFH7446 Power MOSFETS for the inverter circuit
3 Silicon Labs Si8230 isolated dual drivers
An LDO to generate the 3.3 V required by the MCU board
50 m current sensing resistor rated for 10 W
Motor terminal blocks to allow user to attach their own motor
Resistor divider to generate attenuated motor voltage supply (VMDC) - allows MCU to determine if motor supply voltage is high enough for safe operation
Resistor dividers to generate attenuated motor phase voltages with a small positive offset voltage (VMA,VMB,VMC)
Resistor network to generate attenuated sum of motor phase voltages with a small positive offset voltage (VMY)
参考设计MCU板
The MCU board consists of the following:
C8051F850-A-GU QSOP-24 package
2 push-buttons
3 controllable LEDs
1 rotary variable resistance potentiometer
Op-amp to amplify and bias the current sense voltage
USB Hub to support:
C2 USB debug interface
CP2103 USB-UART bridge operating at 115200 baud
CP2112 USB-I2C bridge
Configurable jumpers to select either Hall-sensored or sensorless mode of operation
Test points for connecting to gate drive of user powertrain board and motor.

图5. 参考设计动力板电路图(1)

图6. 参考设计动力板电路图(2)

图7. 参考设计动力板电路图(3)

图8. 参考设计MCU板电路图(1)

图9. 参考设计运放电路图

图10. 参考设计USB桥电路图

图11. 参考设计USB集线器电路图

图12. 参考设计连接器电路图

图13. 低成本BLDC马达设计案例电路图
参考设计动力板材料清单:



参考设计MCU板材料清单:


|
|
|
|
|
|
|